Hinter den Kulissen des Fujitsu Werks in Augsburg
Es gibt noch einen bedeutenden Mainboardhersteller in Europa: Fujitsu in Augsburg. PC Magazin Professional hat die Fertigungsstätte besucht und dabei die Entwicklung und Entstehung eines Mainboards verfolgt.
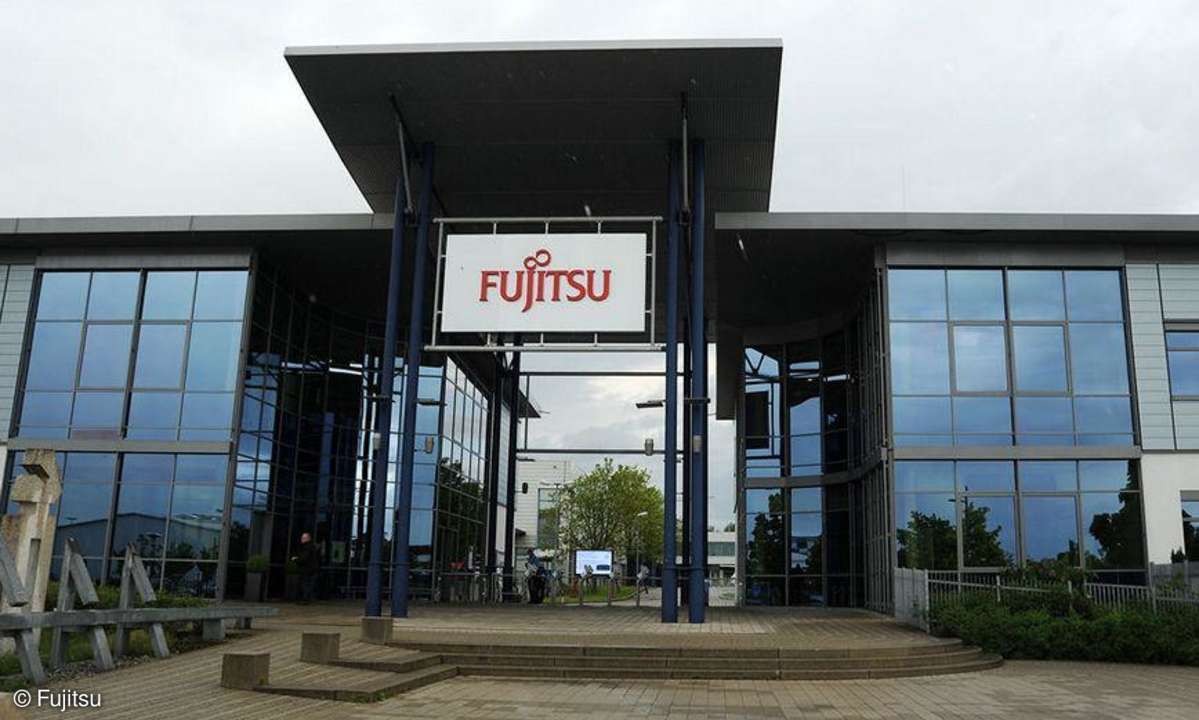
Fujitsu Werk in Augsburg
Es gibt noch einen bedeutenden Mainboardhersteller in Europa: Fujitsu in Augsburg. PC Magazin Professional hat die Fertigungsstätte besucht und dabei die Entwicklung und Entstehung eines Mainboards verfolgt.
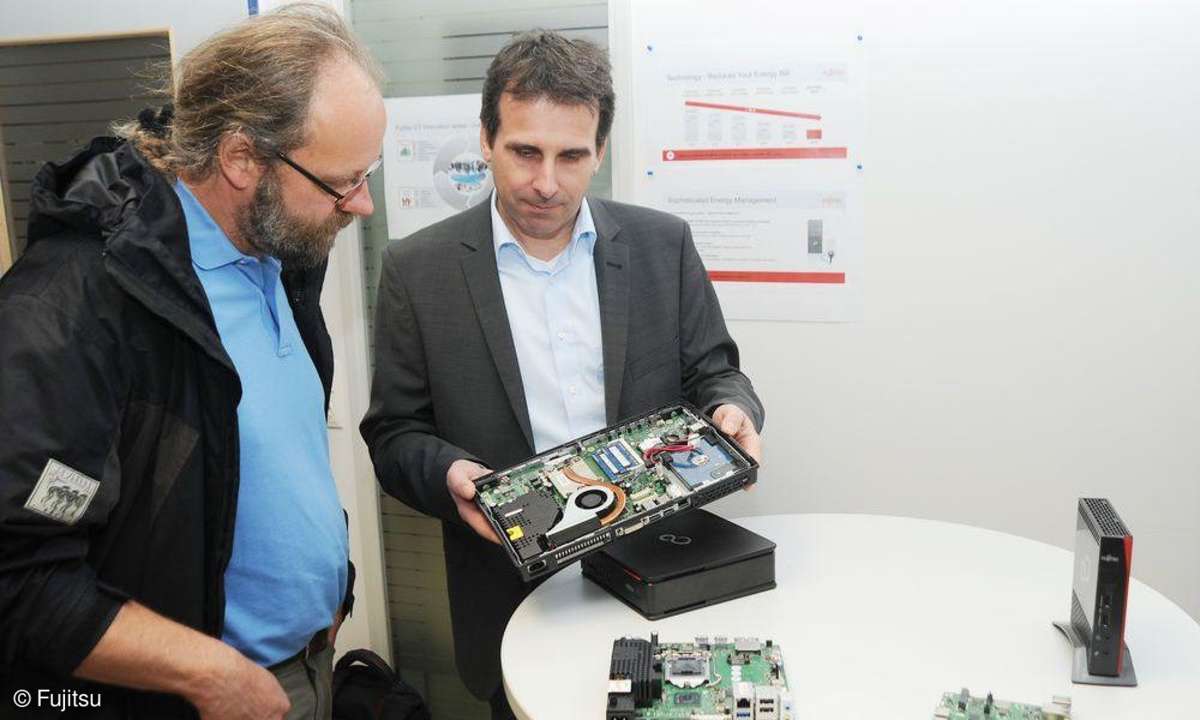
Fujitsu Werk in Augsburg
Neben Mainboards in Standard-Formfaktoren stellt Fujitsu auch spezielle Boards für eigene Rechner her, etwa den Mini-PC Esprimo Q920 oder den All-in-One-PC Esprimo X923. Bei ihnen ist das Netzteil auf dem Board integriert.
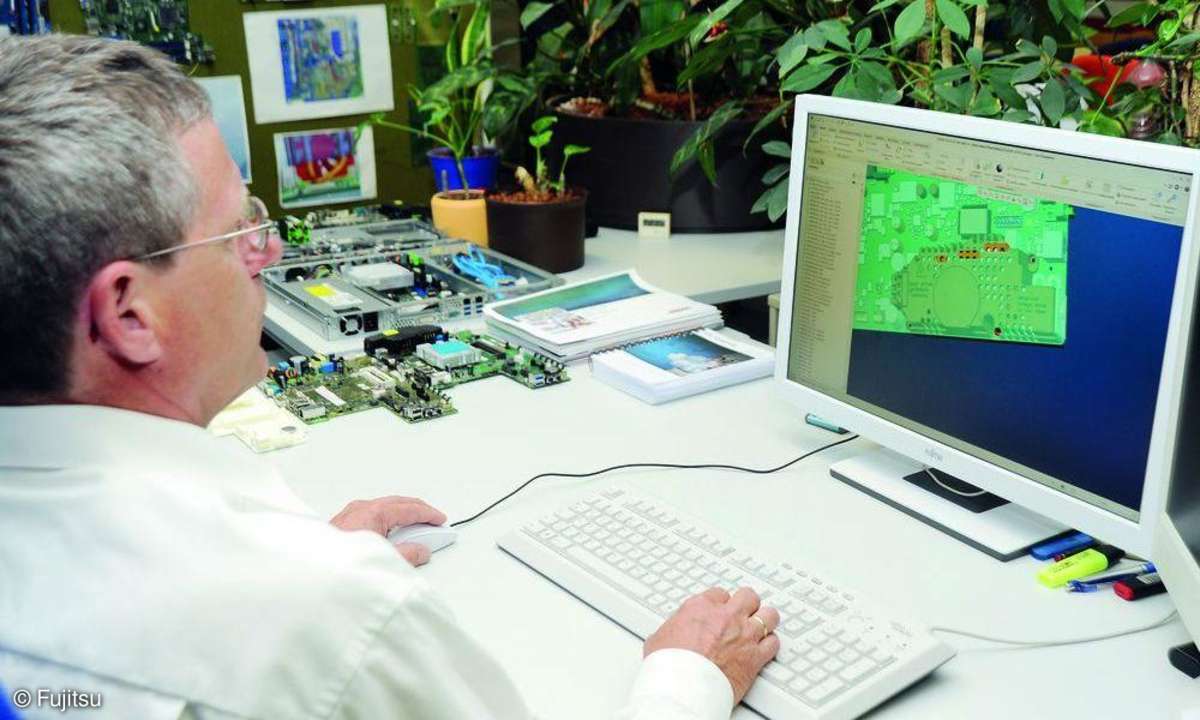
Fujitsu Werk in Augsburg
Einer der ersten Schritte bei der Mainboard-Entwicklung ist die mechanische Konstruktion. Hier wird ein CAD-Modell des Boards erstellt, das in Zusammenarbeit mit dem Mainboard-Layout immer detaillierter wird.
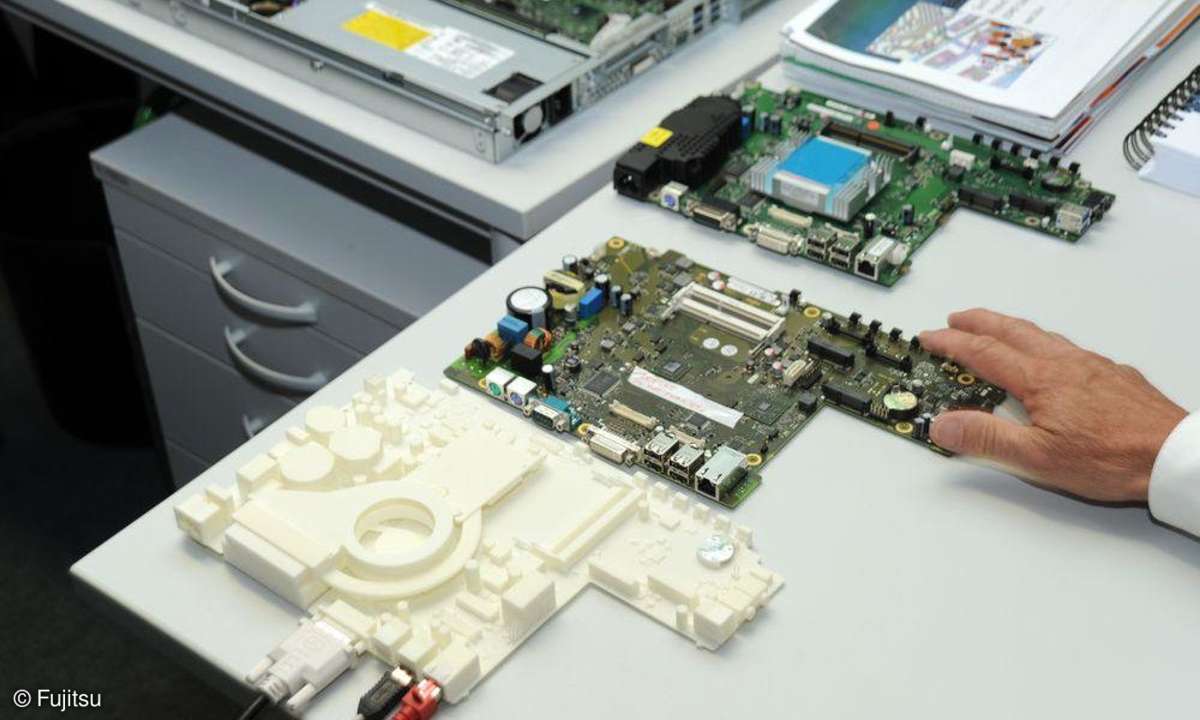
Fujitsu Werk in Augsburg
Vor dem Bau der ersten Prototypen erstellt die mechanische Konstruktion Modelle per 3D-Druck. Mit ihnen kann dann die PC-Entwicklung beim Gehäusedesign arbeiten.
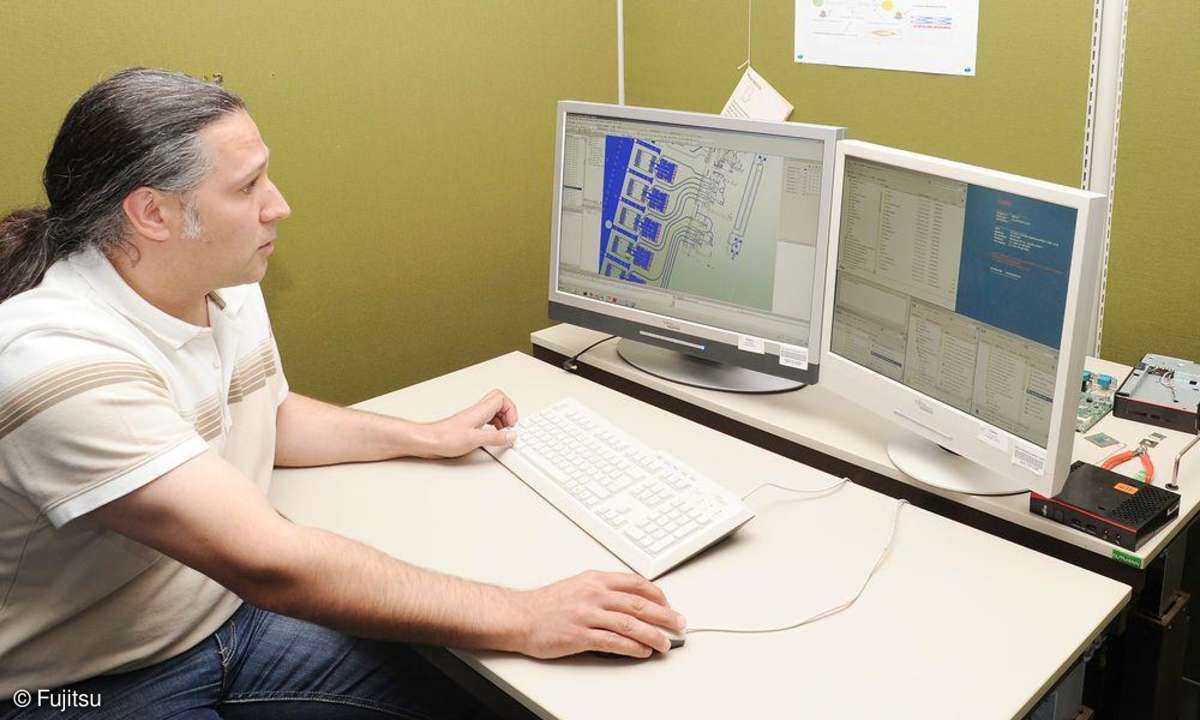
Fujitsu Werk in Augsburg
Gleichzeitig wird der Stromlaufplan für das neue Mainboard erstellt, Fujitsu nutzt dafür die Software Mentor DxDesigner. In ihr werden alle benötigten Schaltungen und Komponenten definiert.
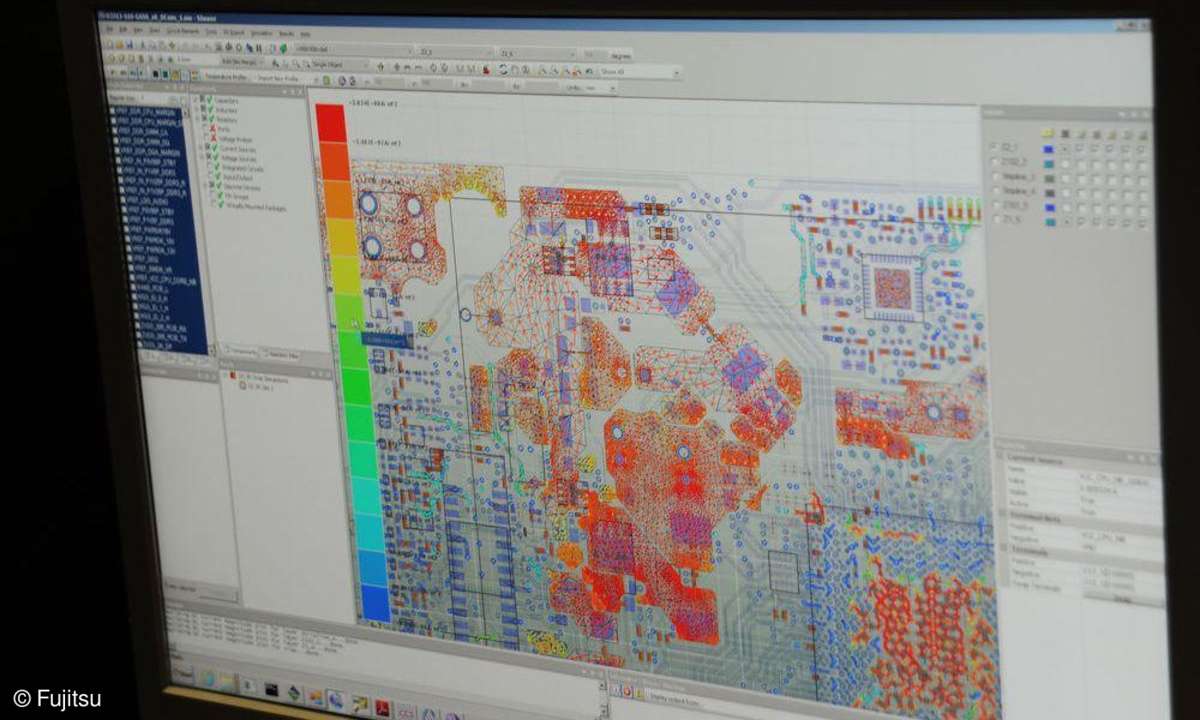
Fujitsu Werk in Augsburg
Bereits während dem Entwurf des Strtomlaufplans werden einzelne Schaltungen simuliert, um Probleme bei der Spannungsversorgung oder der Signalübertragung zu vermeiden.
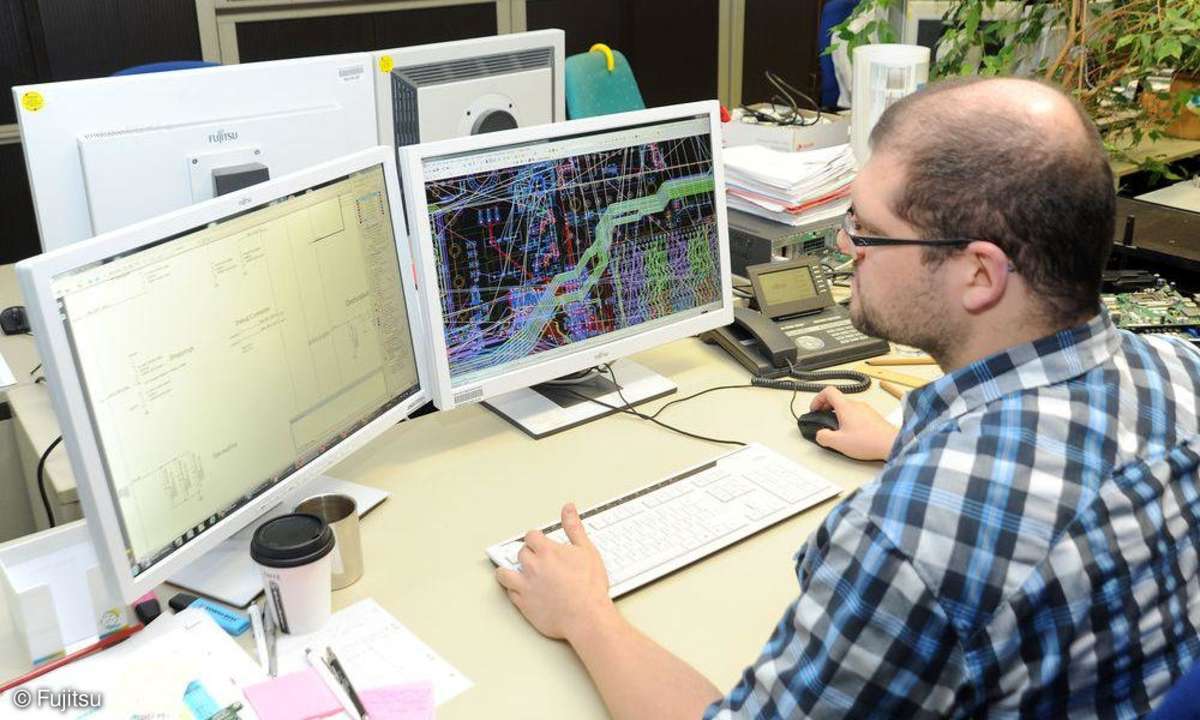
Fujitsu Werk in Augsburg
Mit den Daten aus dem Stromlaufplan beginnt die Arbeit am PCB-Layout. Der Entwickler platziert die durch den Stromlaufplan definierten Komponenten mit dem Layout-Design-CAD-Tool Mentor Expedition auf der virtuellen Platine (Floorplanning). Anschließend werden die Leiterbahnen zwischen den Komponenten unter Berücksichtigung der elektrischen Anforderungen kreuzungsfrei verlegt (Entflechten).
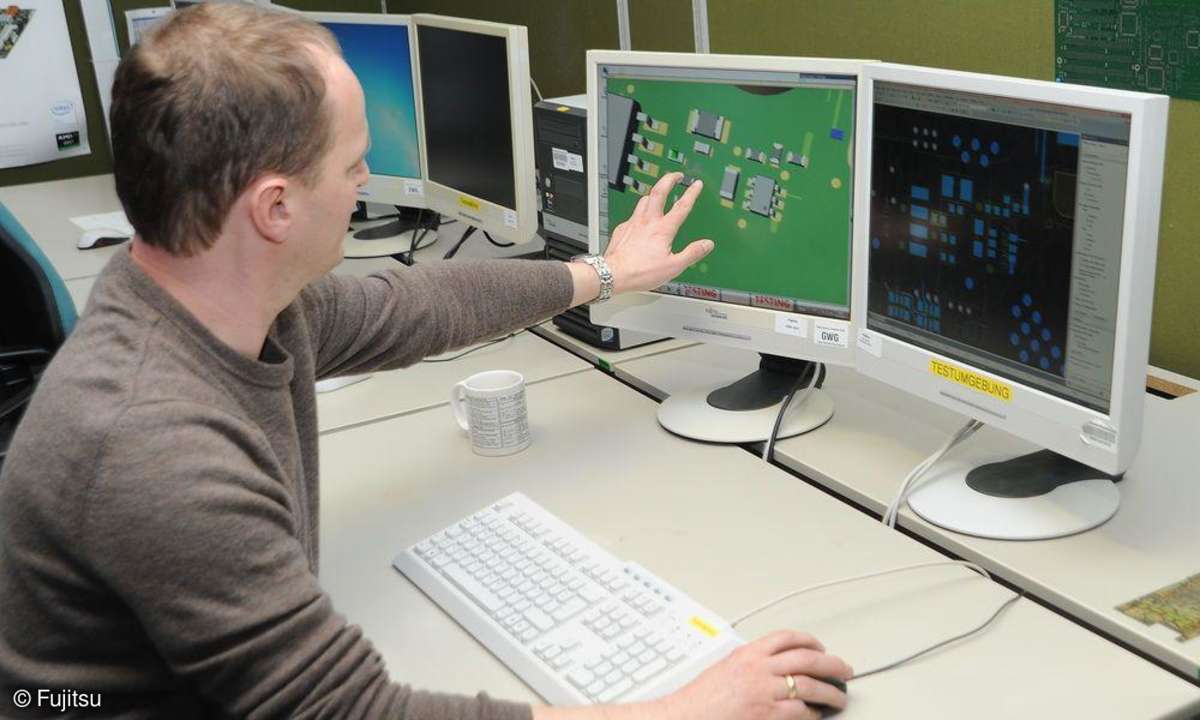
Fujitsu Werk in Augsburg
Hier wird eine neue Software für das PCB-Layout erprobt, die mit 3D-Modellen der Bauteile arbeitet, um so etwa Konflikte mit Komponenten wie dem Kühler auszuschließen. Immerhin muss das hier zu sehende Board im Fuß eines All-in-One-Rechners Platz finden.
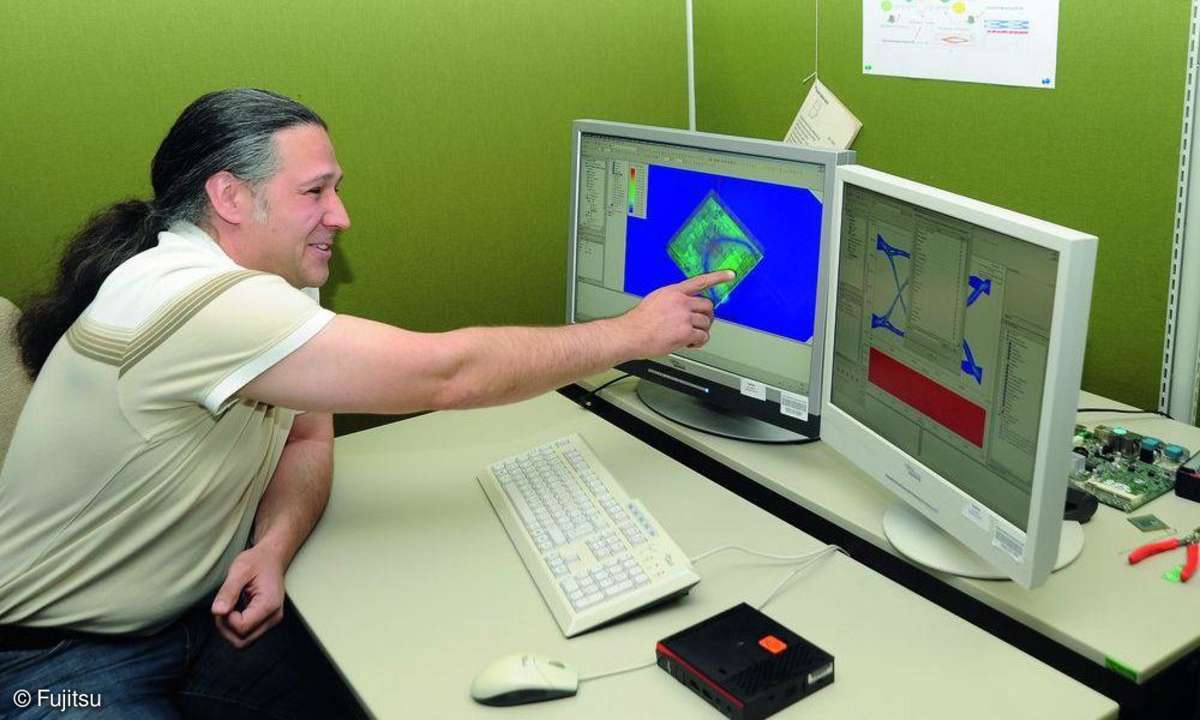
Fujitsu Werk in Augsburg
Auf leistungsfähigen Workstations wird die Funktion der künftigen Mainboards simuliert, um schon vor dem Prototypenbau mögliche Fehler zu finden. Hier ist die EMV-Simulation eines kompletten Rechners zu sehen.
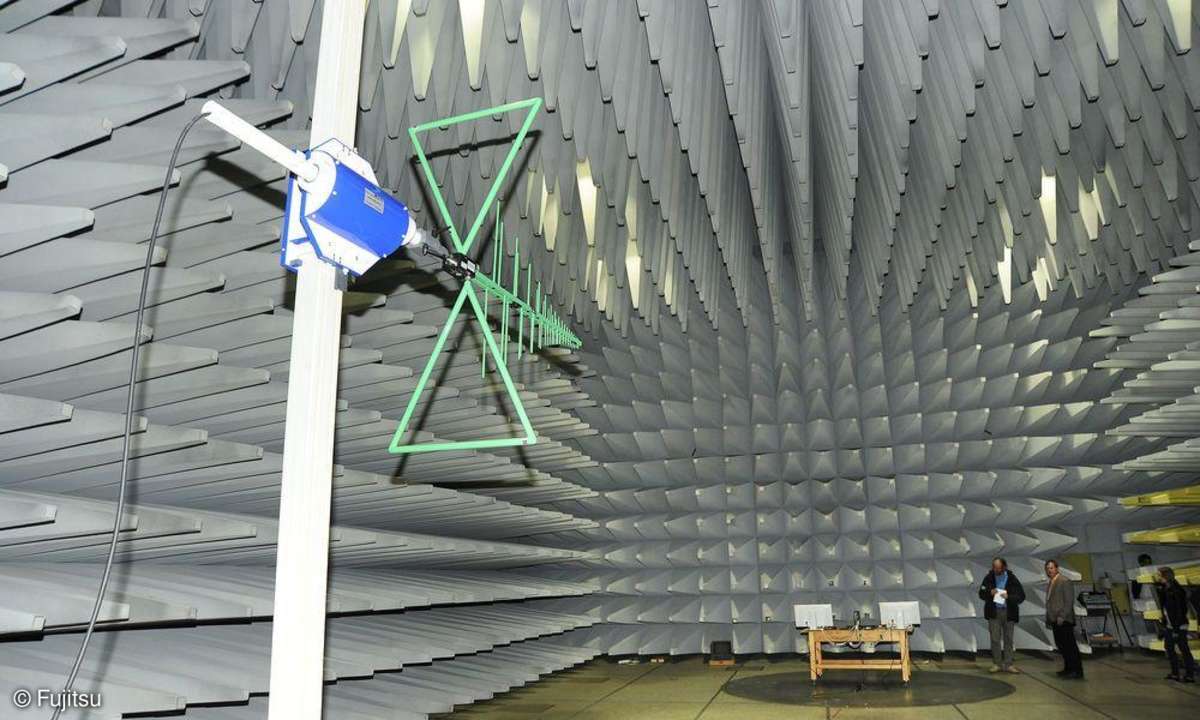
Fujitsu Werk in Augsburg
Fujitsu verfügt in Augsburg über eine große Messhalle für EMV-Tests. Hier werden schon während der Entwicklung neuer Rechner die Ergebnisse der Simulationen mit der Realität verglichen.
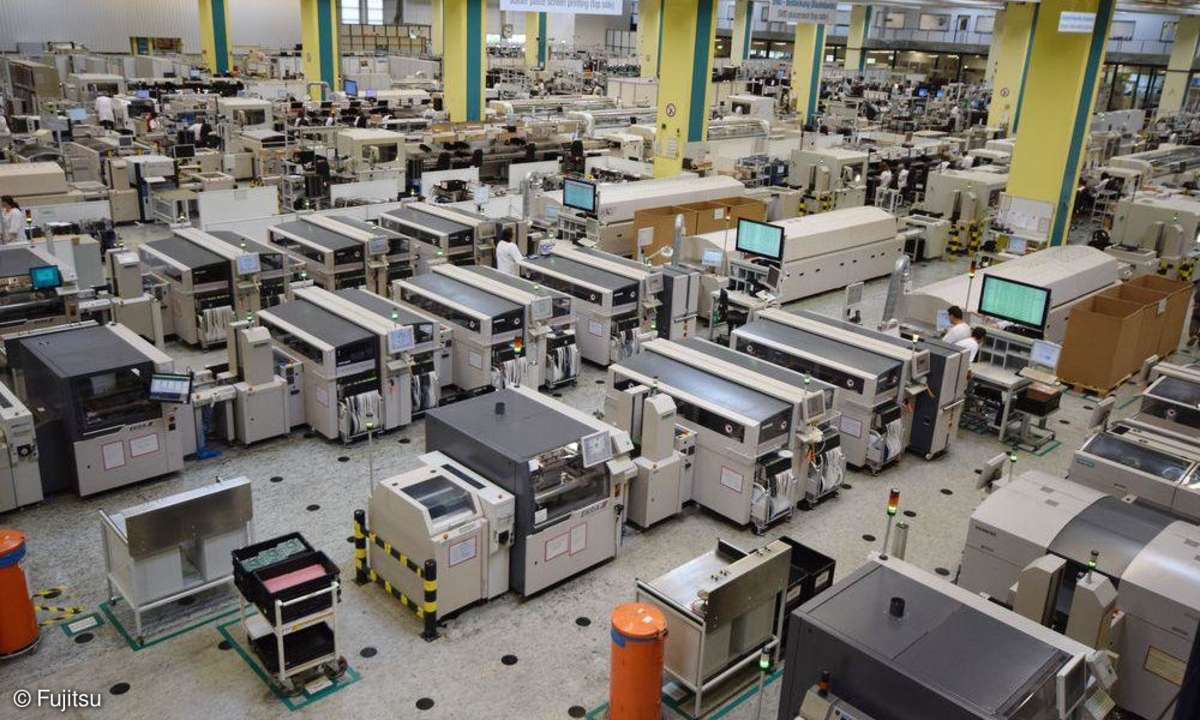
Fujitsu Werk in Augsburg
Mainboardfertigung: Insgesamt sind im Augsburger Fujitsu-Werk sieben komplette Produktionslinien aktiv, die zusammen bis zu 8500 Boards pro Tag produzieren können.
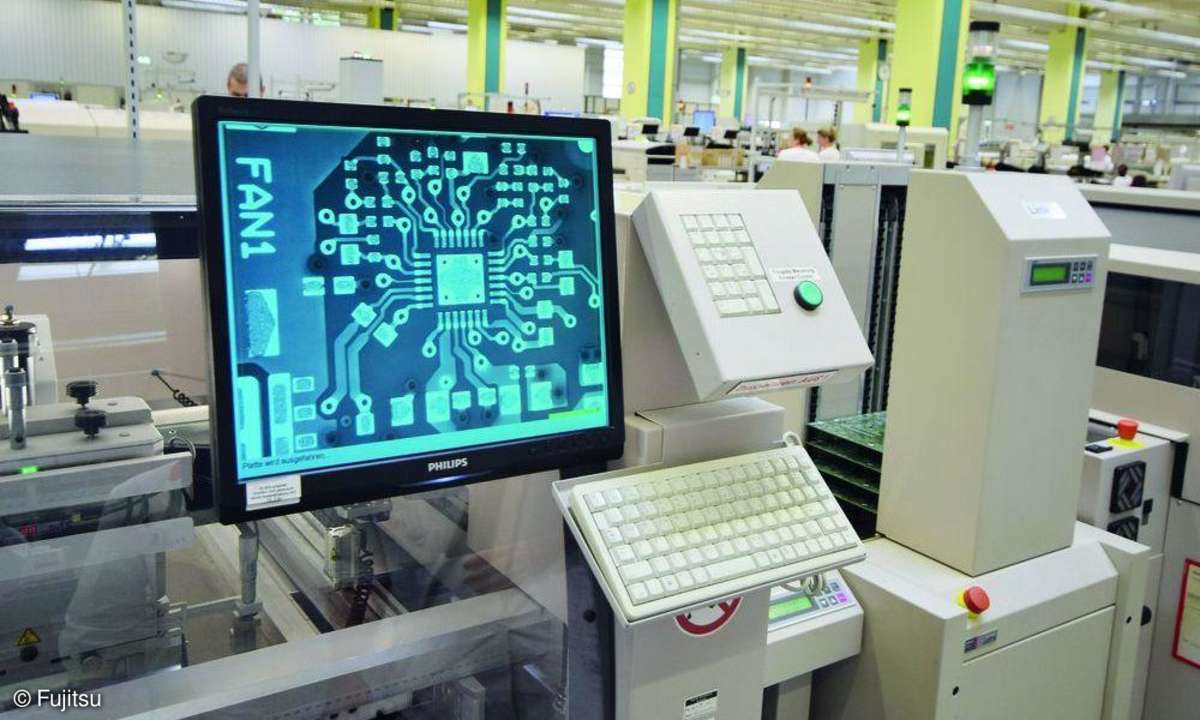
Fujitsu Werk in Augsburg
Im ersten Produktionsschritt wird in einem Schablonendruckverfahren Lotpaste auf die Lotpads für die SMD-Bauteile (Surface-Mounted Device) aufgebracht, das Ergebnis wird von einem automatischen Kamerasystem kontrolliert.
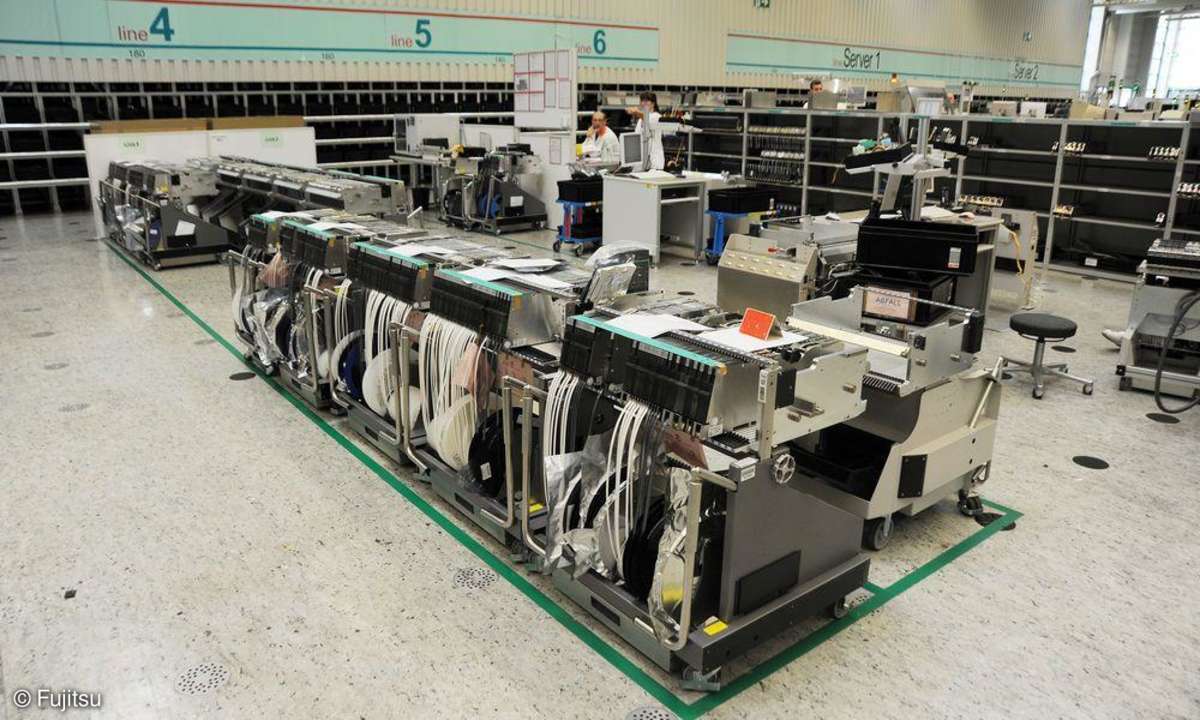
Fujitsu Werk in Augsburg
Die SMD-Komponenten die kleinsten davon, sind gerade einmal 0,6 x 0,3 Millimeter groß, werden auf Rollen mit Kunststoffbändern angeliefert, die dann in Feeder eingelegt werden. Ein Rüstwagen mit bis zu 40 Feedern versorgt den Bestücker mit Bauteilen.
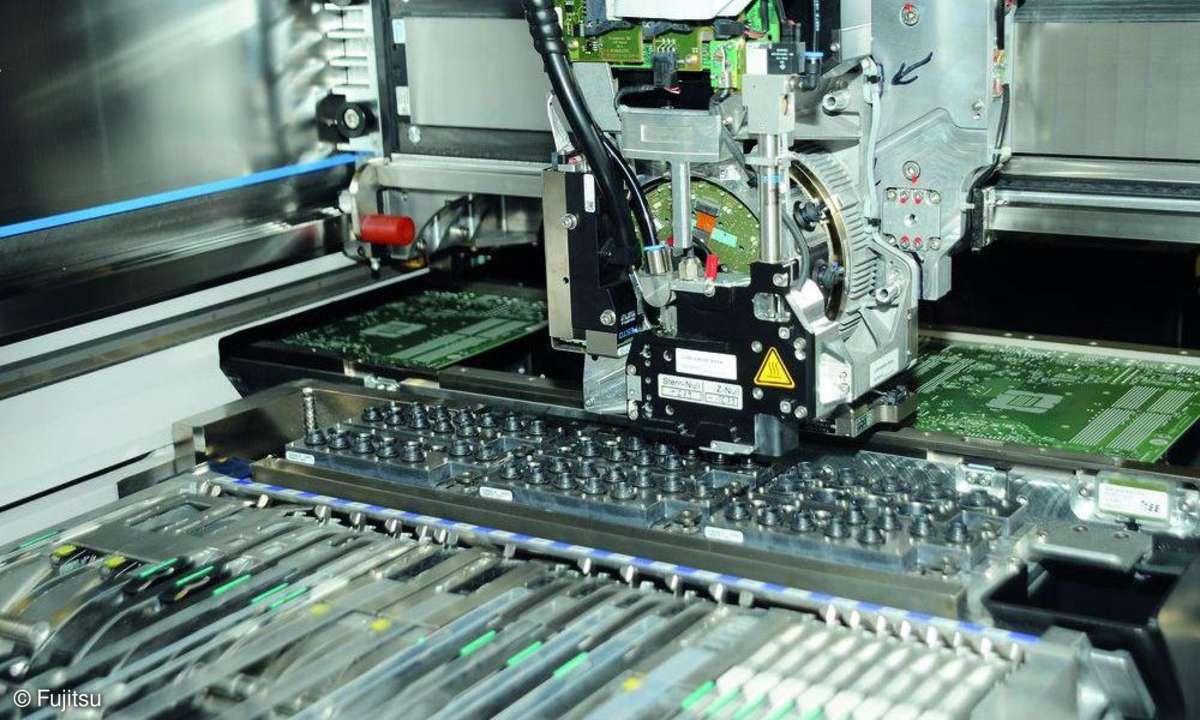
Fujitsu Werk in Augsburg
Im Bestücker nimmt eine rotierende Walze mit 20 Vakuum-Pipetten die SMD-Bauteile auf, überprüft sie mit einer Kamera und setzt sie auf dem richtigen Lotpad ab. Das geht rasend schnell, der Bestücker platziert bis zu 80000 Bauelemente pro Stunde.
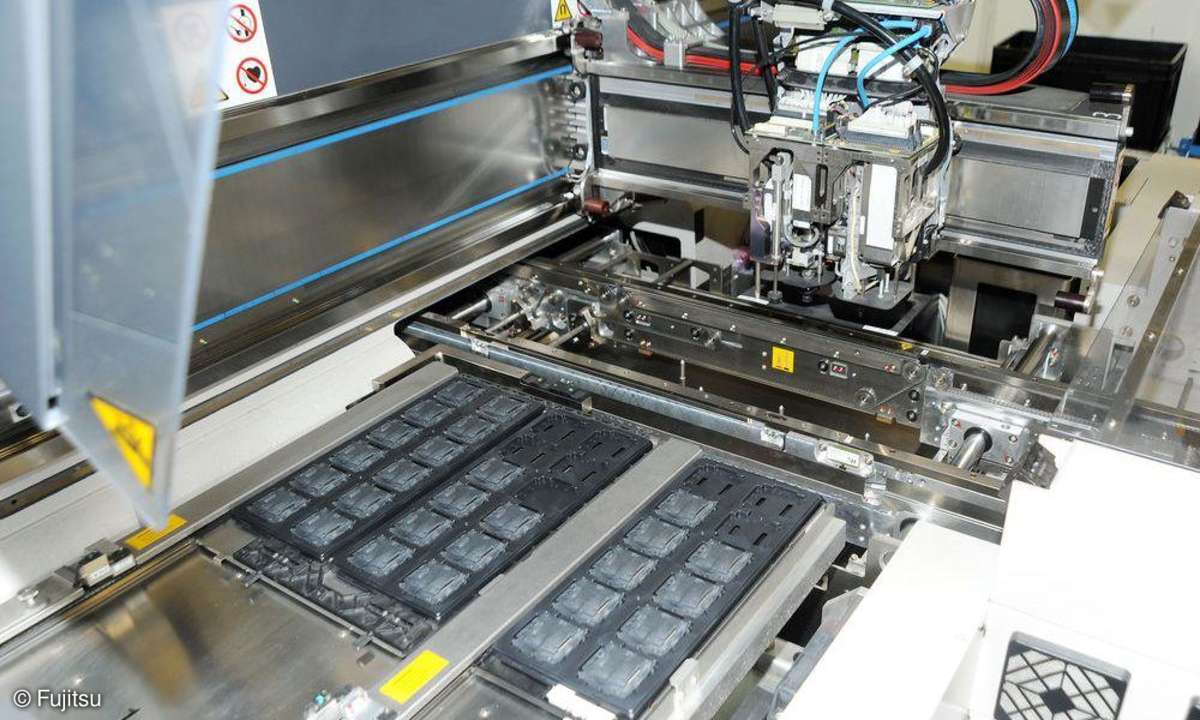
Fujitsu Werk in Augsburg
Weitere Bestückautomaten montieren größere Bauteile wie den Chipsatz oder hier den Prozessorsockel.
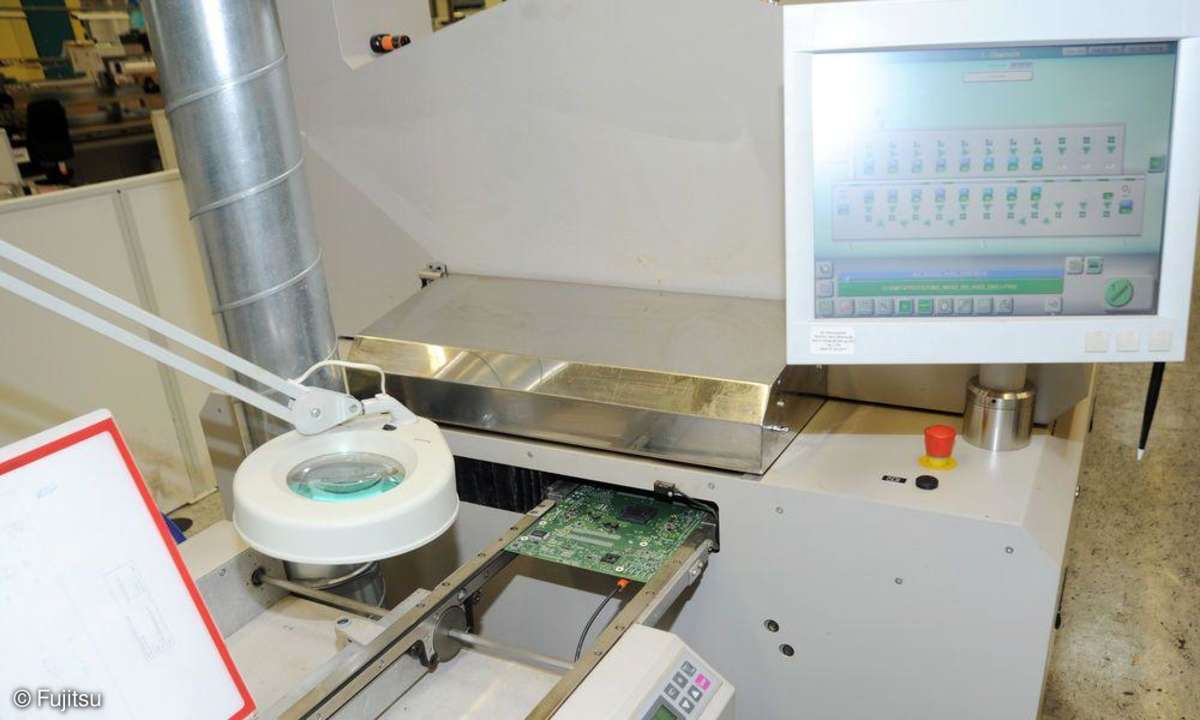
Fujitsu Werk in Augsburg
Danach wird die Platine, die SMD-Elemente haften auf der Lotpaste, in den Reflow-Ofen bewegt.Fujitsu verwendet Vollkonvektionssysteme von SMT, in denen Stickstoff auf bis zu 250 Grad erhitzt wird und mit einem Düsensystem an die zu lötenden Bauteile geführt wird. Durch die Hitze schmilzt das Lot, die Pins der Bauteile verbinden sich fest mit den entsprechenden Pads.
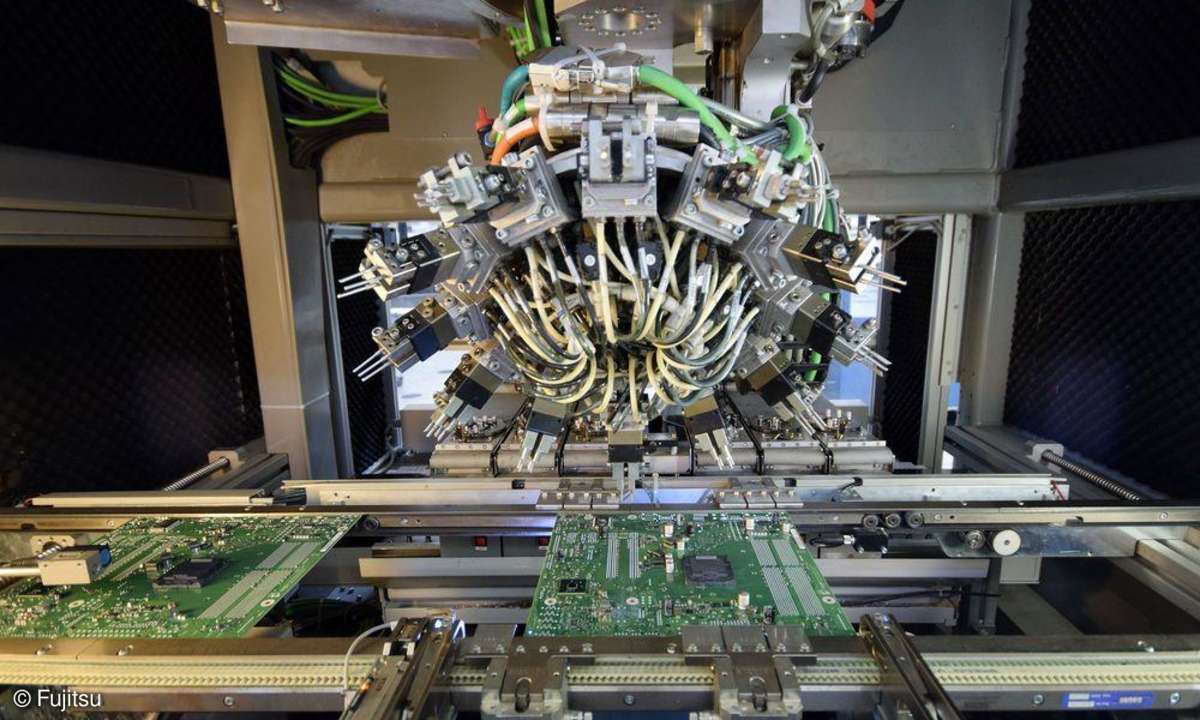
Fujitsu Werk in Augsburg
Selbst 2 polige THT Kondensatoren werden bei Fujitsu automatisch bestückt. Das geht nicht nur schneller als von Hand, auch eine Verpolung wird ausgeschlossen.
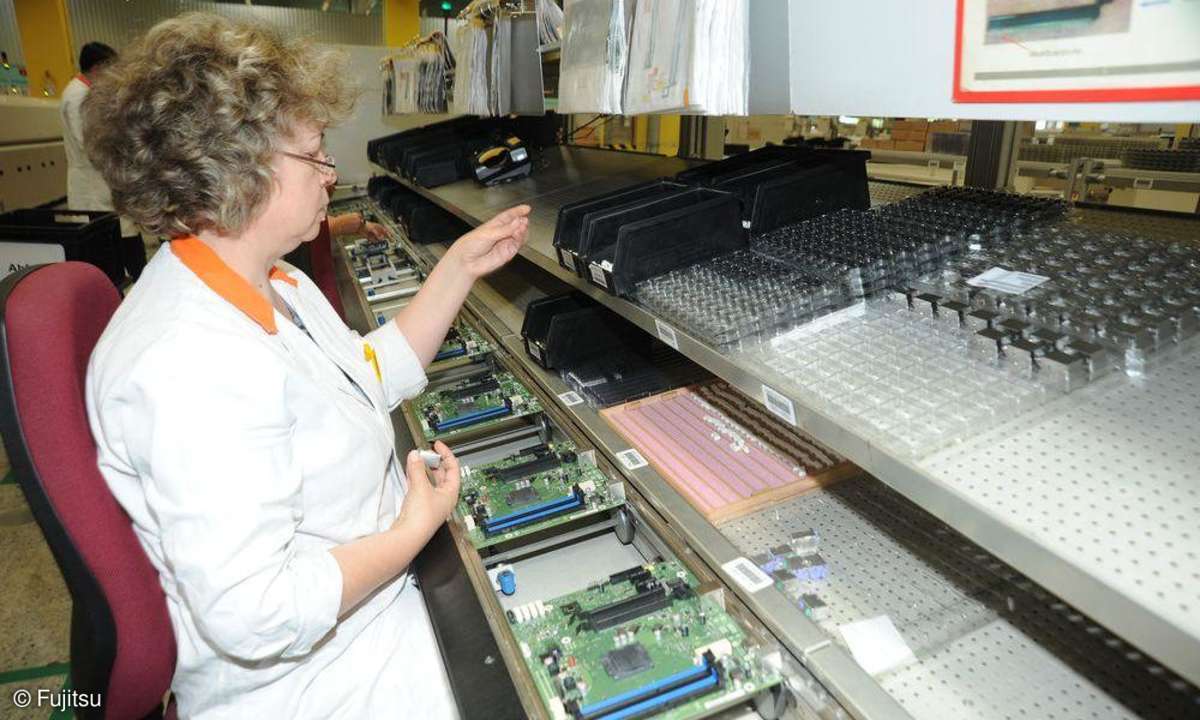
Fujitsu Werk in Augsburg
Einige große Bauteile wie die Speichersockel, die Slots für Steckkarten und die diversen Schnittstellen werden noch von Hand bestückt, man spricht hier von Durchsteckmontage (Through-Hole Technology).
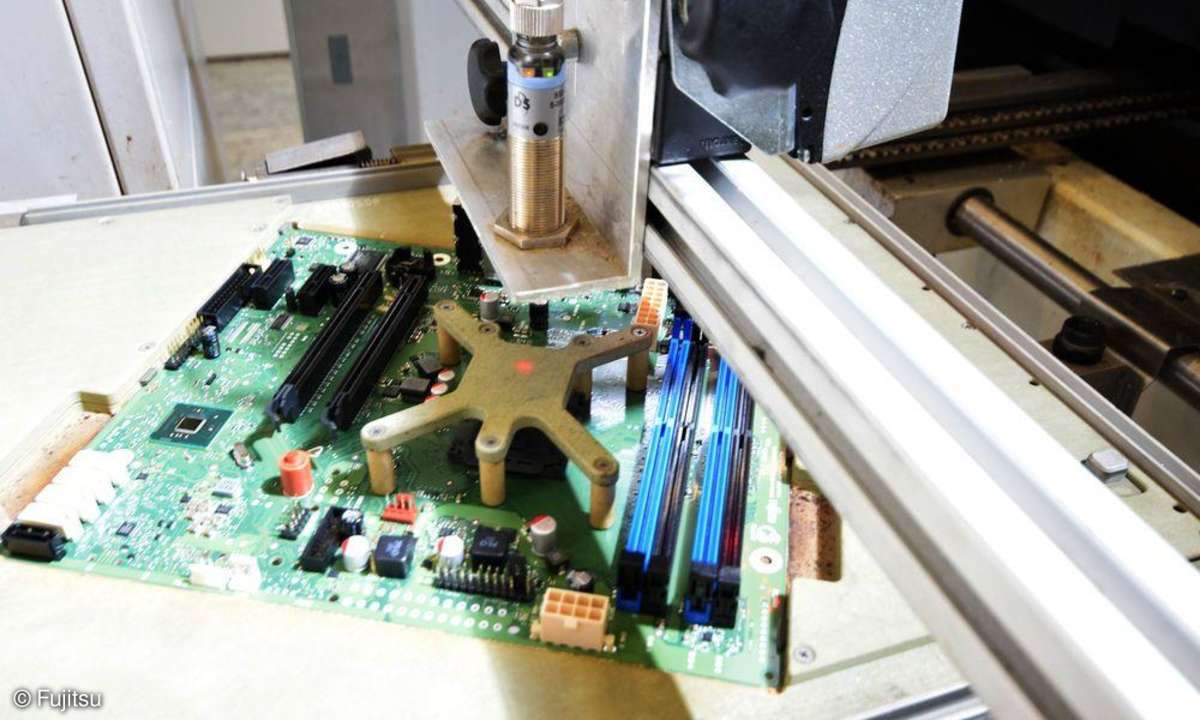
Fujitsu Werk in Augsburg
Nach dem Bestücken laufen die Boards in die Wellenlötanlage. Auch hier erfolgt das Löten unter Stickstoff. Vor dem Löten wird die Position der Boards mit einem Laser überprüft.
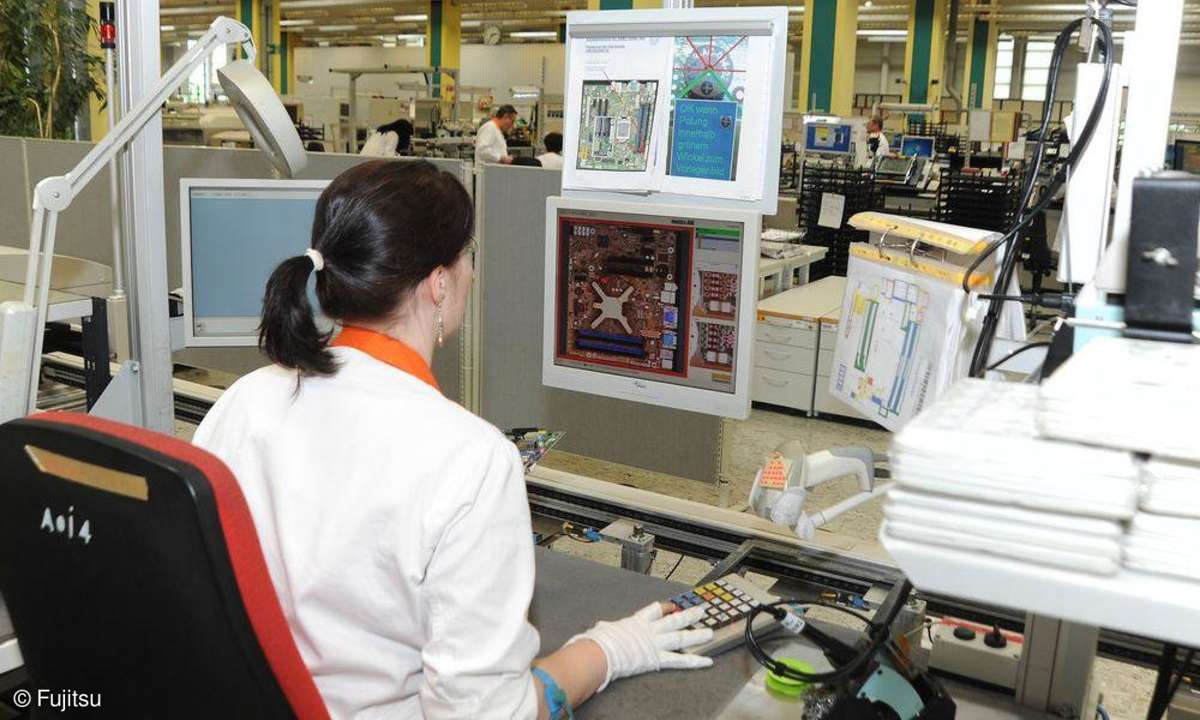
Fujitsu Werk in Augsburg
Die fertigen Mainboards werden von einem Scanner abgelichtet und das Ergebnis mit einer Vorlage verglichen. Abweichungen wie fehlende Komponenten oder Lotbrücken werden erkannt und gleich behoben.
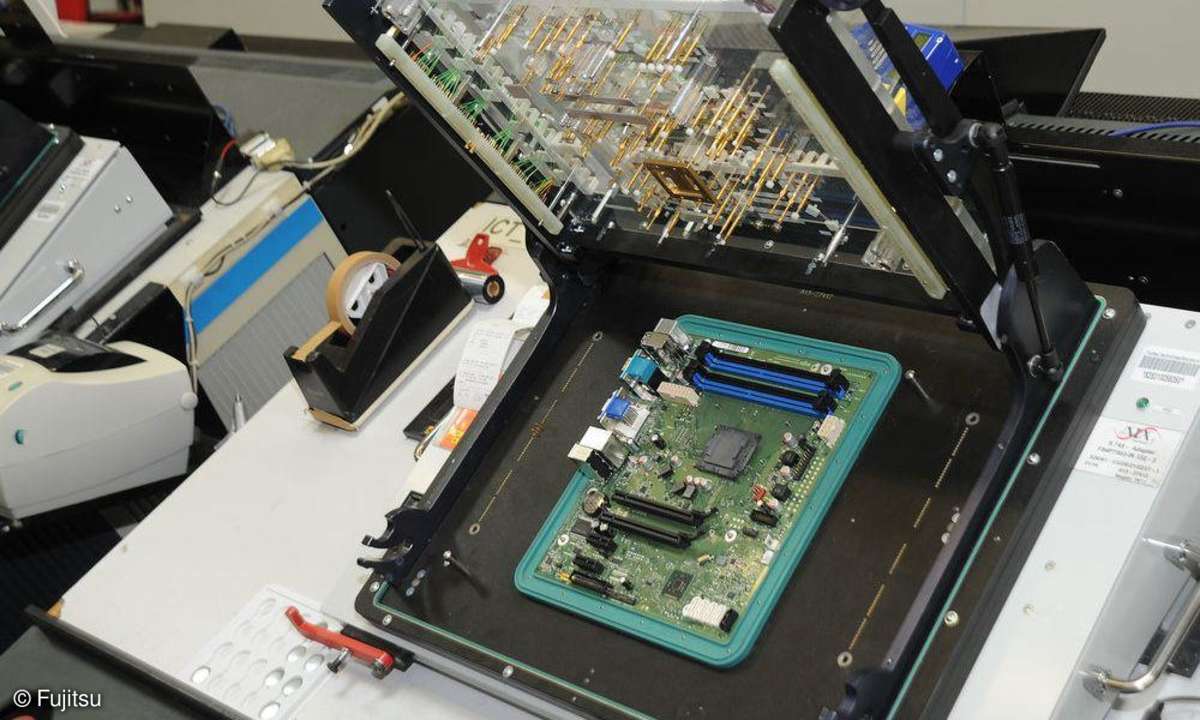
Fujitsu Werk in Augsburg
Danach folgt der elektrische Test in einem speziellen Testadapter, der mit 2000 Nadeln über sogenannte Prüfpunkte auf der Leiterplatte einen elektrischen Kontakt herstellt.
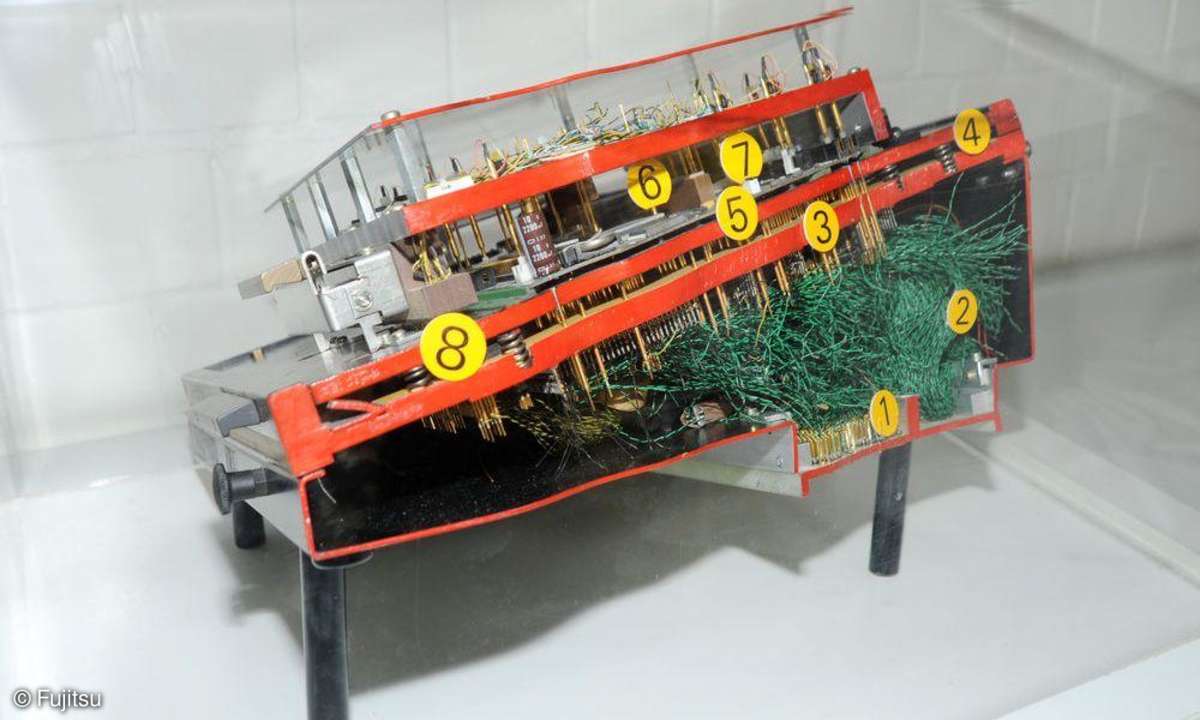
Fujitsu Werk in Augsburg
Hier ist das Schnittmodell eines Prüfadapters zu sehen.
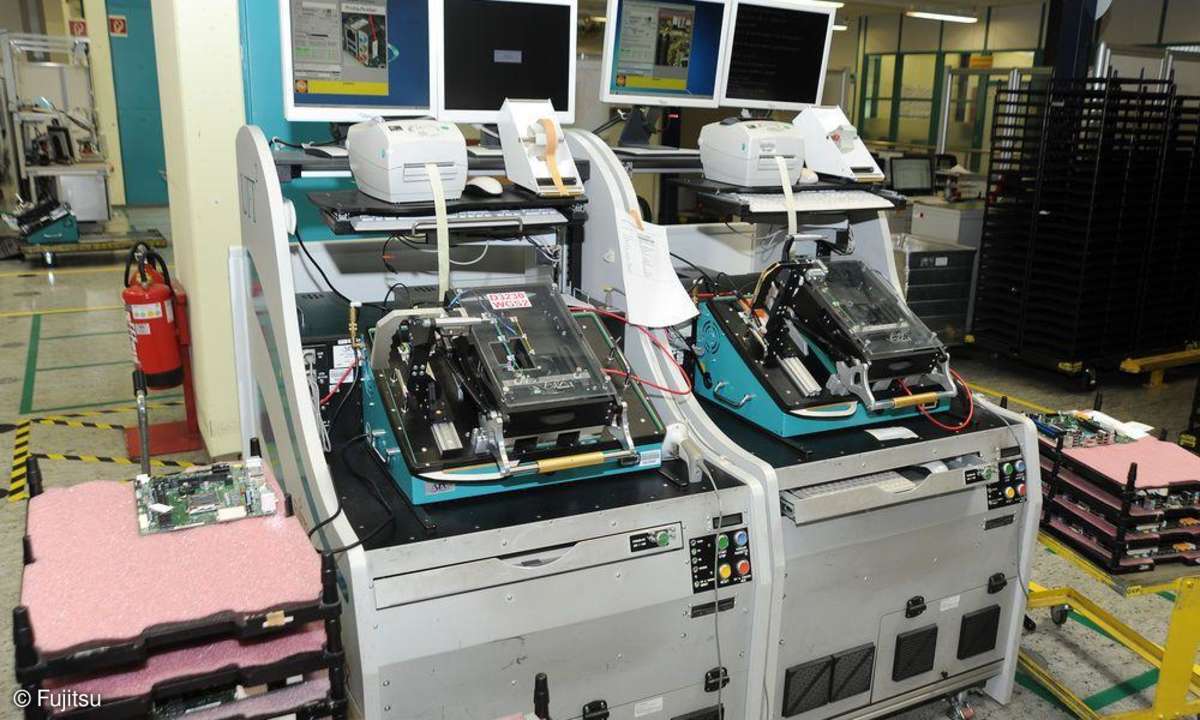
Fujitsu Werk in Augsburg
Als letzter Schritt erfolgt der Funktionstest. Jedes Board wird mit CPU und Speicher bestückt, danach laufen einige Testprogramme, und Windows wird gebootet. Auch BIOS-Optionen werden hier eingestellt.
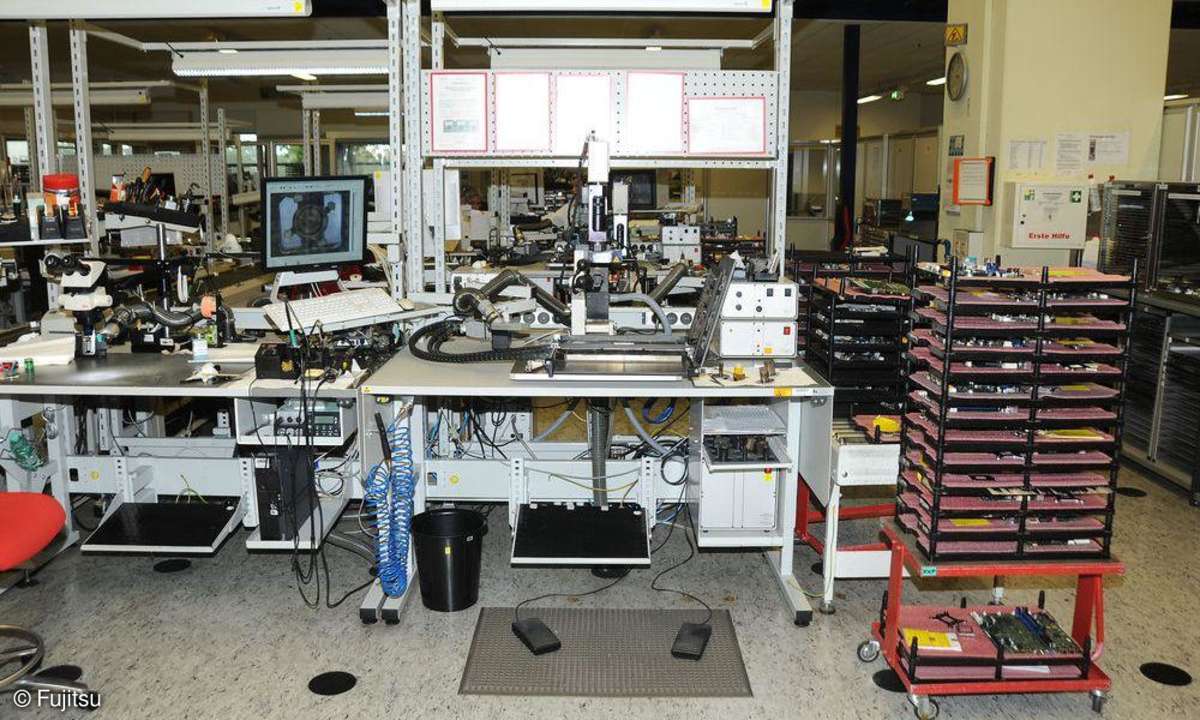
Fujitsu Werk in Augsburg
Fällt tatsächlich einmal eine Hauptplatine durch die diversen Tests, dann wird sie in einer eigenen Reparaturzelle instand gesetzt.